Werksbesuch: Vom Rohstoff zur Feinsteinzeugfliese
Bei Casalgrande Padana haben wir uns nach dem Herstellungsprozess des natürlichen Werkstoffs Feinsteinzeug erkundigt.
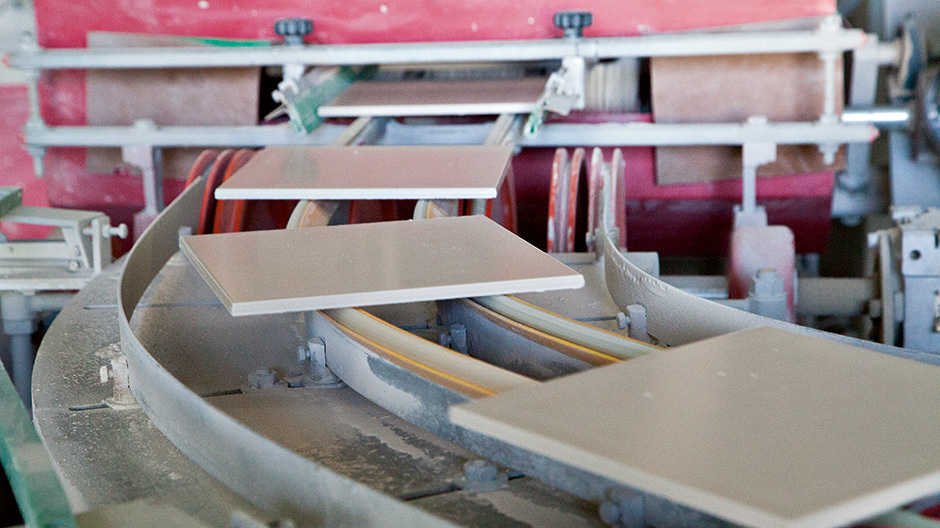
Unser Werksbesuch bei Casalgrande Padana hinterleuchtet die Herstellungsprozesse des Bauprodukts Feinsteinzeug. Welche Formate im Trend liegen und außerdem: Welche Erfindung die Italiener zum heutigen Weltmarkführer für diesen Werkstoff gemacht hat.
Feinsteinzeug als Werkstoff ist schon Jahrhunderte alt. Doch erst die italienische Erfindung eines neuartigen Brennofens sorgte für die revolutionäre Entwicklung eines Materials, das in der Architektur seitdem völlig neue ästhetische und funktionale Möglichkeiten eröffnete. Die mittelitalienischen Städte Casalgrande, Sassuollo und Castellarano wurden seither zum Weltzentrum der Fliesenherstellung und die italienischen Hersteller zu den wesentlichen Treibern in der weiteren Entwicklung dieses Werkstoffs.
Erfindung des Feinsteinzeugs
1706 waren es Johann Friedrich Böttger und Ehrenfried Walther von Tschirnhaus, die einen neuartigen keramischen Werkstoff erfanden. Ihr rotbraunes Feinsteinzeug ist durch den Brennvorgang vollständig durchgesintert und hat deshalb eine äußerst geringe Wasseraufnahmefähigkeit. Für den Einsatz im Baugewerbe bedeutet dies: Es ist absolut frostbeständig. In den 1980er-Jahren entwickelten italienische Firmen das Schnellbrand-Rollenofen-Verfahren. Damit wurde es möglich, Feinsteinzeug als Fliesen herzustellen. Und die speziellen Produkteigenschaften sorgten dafür, dass Feinsteinzeugfliesen sehr rasch eine enorme Bedeutung errangen. Denn die Fliesen sind sehr abriebfest, bruchfest und durchgefärbt. Sie bestehen aus nur drei Rohmaterialien, deren Mischungsverhältnis Farbe und Textur des Scherbens bestimmen.
Hatte das ursprünglich „rotbraune Feinsteinzeug“ seine Färbung von Eisenanteilen im Rohstoff, so werden inzwischen hochreine Rohmaterialien verwendet, die eine weiße Fliese möglich machen. Die verschiedenen Farben werden durch zugesetzte Salze oder farbige Keramikpulver erzeugt. Durch Druckpressen werden nicht nur die Fliesenformate bestimmt, sondern vor allem auch die Oberflächenstruktur. Auf diese Weise wurden die Materialeigenschaften und Fertigungsmethoden genutzt, um unterschiedlichste Naturmaterialien nachzustellen. Am geläufigsten ist die Produktion von Fliesen in der Optik verschiedenster Natursteine – jedoch ohne die produktbedingten Nachteile des Naturmaterials. Inzwischen können auch Hölzer, Textilien und Leder nachgestellt werden.
Das Format wächst
Jahr für Jahr übertreffen sich die italienischen Hersteller gegenseitig mit neuen Weltrekorden in der Fliesendimension. Mittlerweile sind Fliesenformate von 320 auf 160 Zentimeter absolut üblich geworden. Sie sind meist zehn oder nur sieben Millimeter dick. Solche Platten können von geschulten Handwerkern mit Spezialwerkzeugen verlegt werden und ergeben nahezu fugenlose Flächen. Die Großformate werden außerdem an Fassaden eingesetzt, aber auch als Arbeitsplatten oder Möbeloberflächen. Aus den großen Platten werden auch alle anderen geläufigen Fliesenformate geschnitten.
Mit glasfaserverstärktem Rücken können die Großformate mit einer minimalen Dicke von drei Millimetern hergestellt werden. Feinsteinzeugfliesen sind extrem maßhaltig. Sie werden kalibriert und rektifiziert. Die Plattendimensionen werden also durch nachträgliche Bearbeitung hoch exakt, und die Kanten erhalten zusätzlich eine Fase. Auf diese Weise sind minimale Fliesenfugen möglich. Feinsteinzeugplatten können grundsätzlich so verwendet werden, wie sie aus dem Brennofen kommen. Dennoch ist es möglich, die Fliesen vor dem Brand oder anschließend zu individualisieren. Die ungebrannten Fliesen können durch ein Ink-Jet-Druckverfahren mit Dekoren versehen werden. In der Vergangenheit geschah dies mit traditioneller Drucktechnik und mit entsprechend geringen Möglichkeiten der projektbezogenen Individualisierung.
Die neueste Entwicklung der italienischen Fliesenindustrie führte zum Einsatz spezieller Tintenstrahldrucker, die mit vergleichsweise geringem Aufwand das Bedrucken selbst kleinster Fliesenmengen möglich machte. Benötigt wird dazu lediglich ein digitalisiertes Bild. Feinsteinzeugfliesen können außerdem glasiert werden. Im Anschluss an den Brand ist es zusätzlich möglich, die Fliesen zu satinieren, zu schleifen oder zu polieren. Den genauen Fertigungsprozess haben wir uns im Detail angesehen.
In neun Schritten zur fertigen Feinsteinzeugfliese:
1. Die drei Grundstoffe: Tonerde, Feldspat und Sand sind mit einem ungefähren Mischungsverhältnis 40, 40 und 20 Prozent die Hauptelemente von Feinsteinzeug. Die Tonerde kommt normalerweise entweder aus dem Westerwald, der Ukraine oder der Region rund um Lyon. Feldspat kommt aus Sardinien oder wird aus der Türkei importiert, und der Quarzsand kommt aus der italienischen Provinz Kalabrien. Ursprünglich kamen alle Rohstoffe aus Casalgrande in der Region von Sassuolo. Aber die dortigen Vorkommen enthalten Eisen, was die Farbigkeit des Feinsteinzeugs beeinflussen würde. Deshalb werden heutzutage aus aller Welt die reinsten Rohstoffe importiert.
Der Vorteil für Architekten: Feinsteinzeug besteht aus naturreinen Rohstoffen. Als keramisches Produkt birgt es keine Schadstoffrisiken, die bei der Planung berücksichtigt werden müssten.
2. Die Aufbereitung der Rohstoffe: In großen Mühlen wird das Rohmaterial in einem zwei Stunden dauernden Prozess zerkleinert, gemischt und mit Wasser zum sogenannten „Schlicker“ aufgeschlämmt. Dieses Zwischenprodukt enthält 35 Prozent Wasser und wird in drei verschiedenen Weiß-Tönen hergestellt – je nachdem, was für ein Feinsteinzeug schließlich daraus entstehen soll.
3. Das Feinsteinzeug wird farbig: In einem weiteren Produktionsschritt werden die Farben gemahlen. Die Rohstoffe Kobalt, Chrom, Eisen und Mangan werden separat aufbereitet und den unterschiedlichen Feinsteinzeugsorten beigemischt. Es gibt 85 Rezepte zur Herstellung unterschiedlichster Feinsteinzeugfliesen.
Der Vorteil für Architekten: Durch die immer zahlreicheren Rezepturen werden immer mehr Gestaltungsvariationen möglich.
4. Das Granulat entsteht: In einen Sprühturm wird heiße Luft eingeleitet, die den flüssigen Schlicker trocknet und zu einem Granulat werden lässt, das nun noch 5 bis 7 Prozent Feuchtigkeit enthält. Das Granulat wird auf einem Förderband weitertransportiert. Die Abwärme der mit Erdgas betriebenen Sprühtürme wird zur Stromerzeugung genutzt. Das getrocknete Granulat wird aus dem Sprühturm auf ein Förderband geleitet. In 110 Silos werden die verschiedenen Mischungen für die weitere Produktion vorgehalten.
5. Das Pressen der Fliesen: Auf zehn Pressen wird das Granulat weiterverarbeitet. Je nach Fliese werden dabei bis zu zehn Tonnen Druck pro Quadratzentimeter ausgeübt. Durch das Pressen werden Dicke und Oberflächenstruktur der späteren Feinsteinzeugfliesen bestimmt. In diesem Zustand sind sie noch um 5 bis 7 Prozent größer als nach dem Brand. Die Kunst liegt in der vorausschauenden Kalkulation dieses Schwundes. Denn je größer das Format, umso schwieriger ist es, die letztendliche Größe zu berechnen. Die gleichbleibende Qualität der Produktion wird durch Probebrände von Einzelfliesen alle zwei Stunden sichergestellt.
Der Vorteil für Architekten: Allein durch den Anpressdruck entstehen unterschiedlichste Texturen und Formate in stets gleichbleibender und kontrollierter Qualität.
6. Der Druck: Farbe und Struktur der Feinsteinzeugfliesen werden durch Materialmischung und Pressung festgelegt. Sollen die Fliesen zusätzlich eine Musterung bekommen, müssen sie bedruckt werden. Dieser Fertigungsschritt findet vor dem Brand statt. Das Inkjet-Verfahren entspricht im Groben dem eines klassischen Bürodruckers und ist ein gewaltiger Innovationsschritt. Denn beim herkömmlichen Walzenverfahren kostete jede Änderung an der Fliese rund 10.000 €. Beim digitalen Druck sind dagegen projektbezogene Fertigungen jederzeit und mit relativ geringem Aufwand möglich – bis hin zur Einzelfertigung.
Der Vorteil für Architekten: Drucktechnologien ermöglichen die projektbezogene Gestaltung von Feinsteinzeug – selbst in kleinsten Auflagen. Nicht nur Nachbildungen von Naturprodukten werden dadurch möglich, sondern auch die Umsetzung eigener Gestaltungsvorgaben.
7. Der Brennvorgang: Der Brennofen ist 110 Meter lang und produziert 6.000 bis 7.000 Quadratmeter Feinsteinzeugfliesen pro Tag. Der Brennprozess dauert im Schnitt 50 Minuten, wobei es innerhalb des Ofens verschiedene Temperaturzonen gibt. Am Ende werden gerissene Fliesen aussortiert.
8. Der Transport: Vollautomatisch fahrende Wagen transportieren jeweils bis zu 20 Tonnen Fliesen. Wenn bestimmte Produkte noch oberflächenbearbeitet werden sollen, fahren die Roboter sie zum nächsten Produktionsschritt.
9. Qualitätskontrolle: Vollautomatisch werden die Fliesen fotografiert und auf die optische Qualität, auf tadellose Oberfläche, Maßhaltigkeit und Kalibrierung geprüft. Alle zehn Minuten wird die Prüfmaschine ihrerseits durch Qualitätskontrolleure geprüft. Im letzten Fertigungsschritt werden die Feinsteinzeugfliesen verpackt und versandfertig gemacht.
Der Vorteil für Architekten: Die neuesten Fertigungsmethoden garantieren höchste Qualität und perfekte Maßgenauigkeit.
Casalgrande Padana
www.casalgrandepadana.deCeramics of Italy
www.laceramicaitaliana.itMehr Stories
Wenn Möbel Mode machen
Flexible Möbel von USM für dynamische Shop-Konzepte
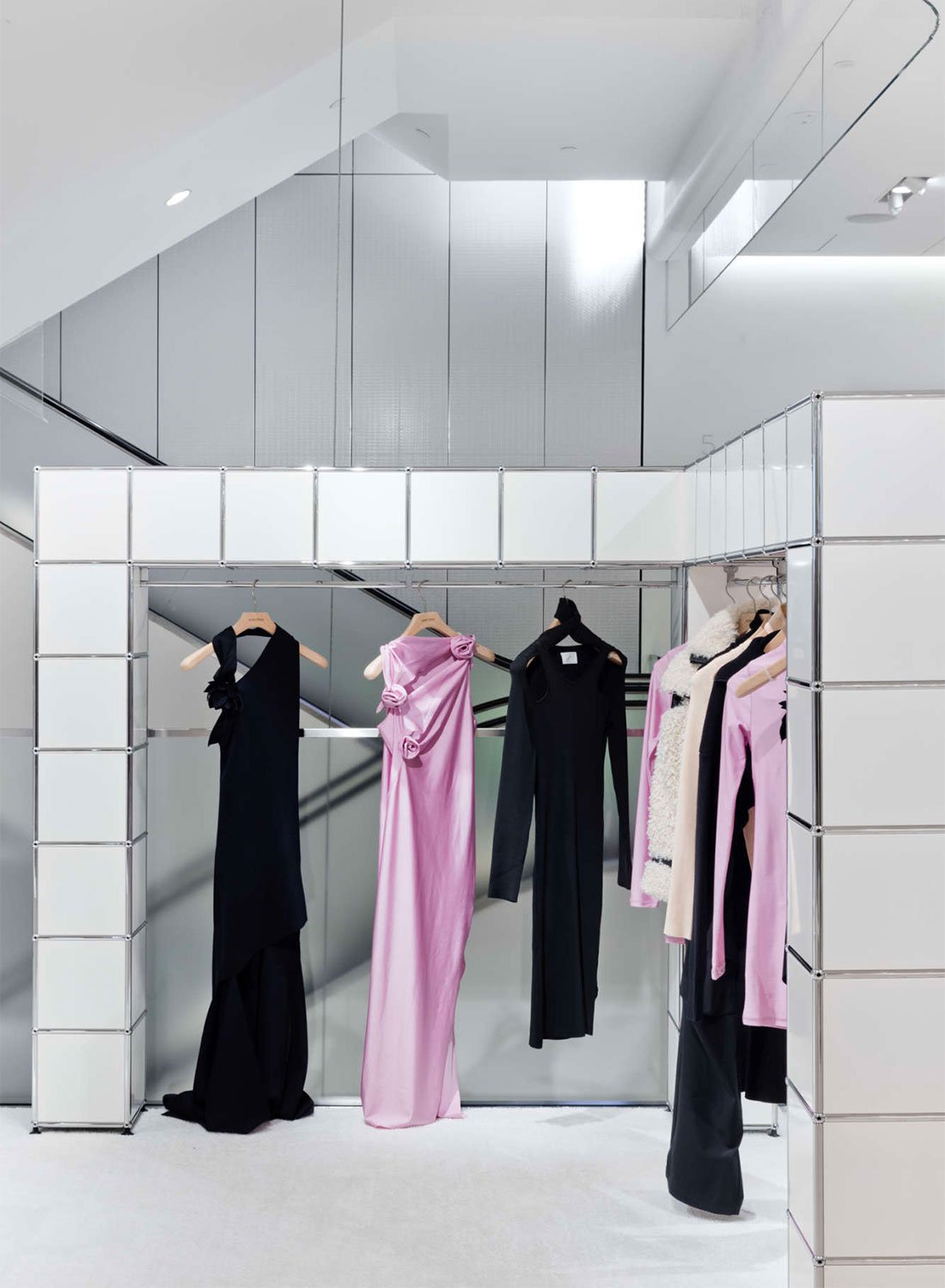
Gezähmtes Grün
Klimafreundliche Pflastersysteme aus dem Steinlabor von Godelmann
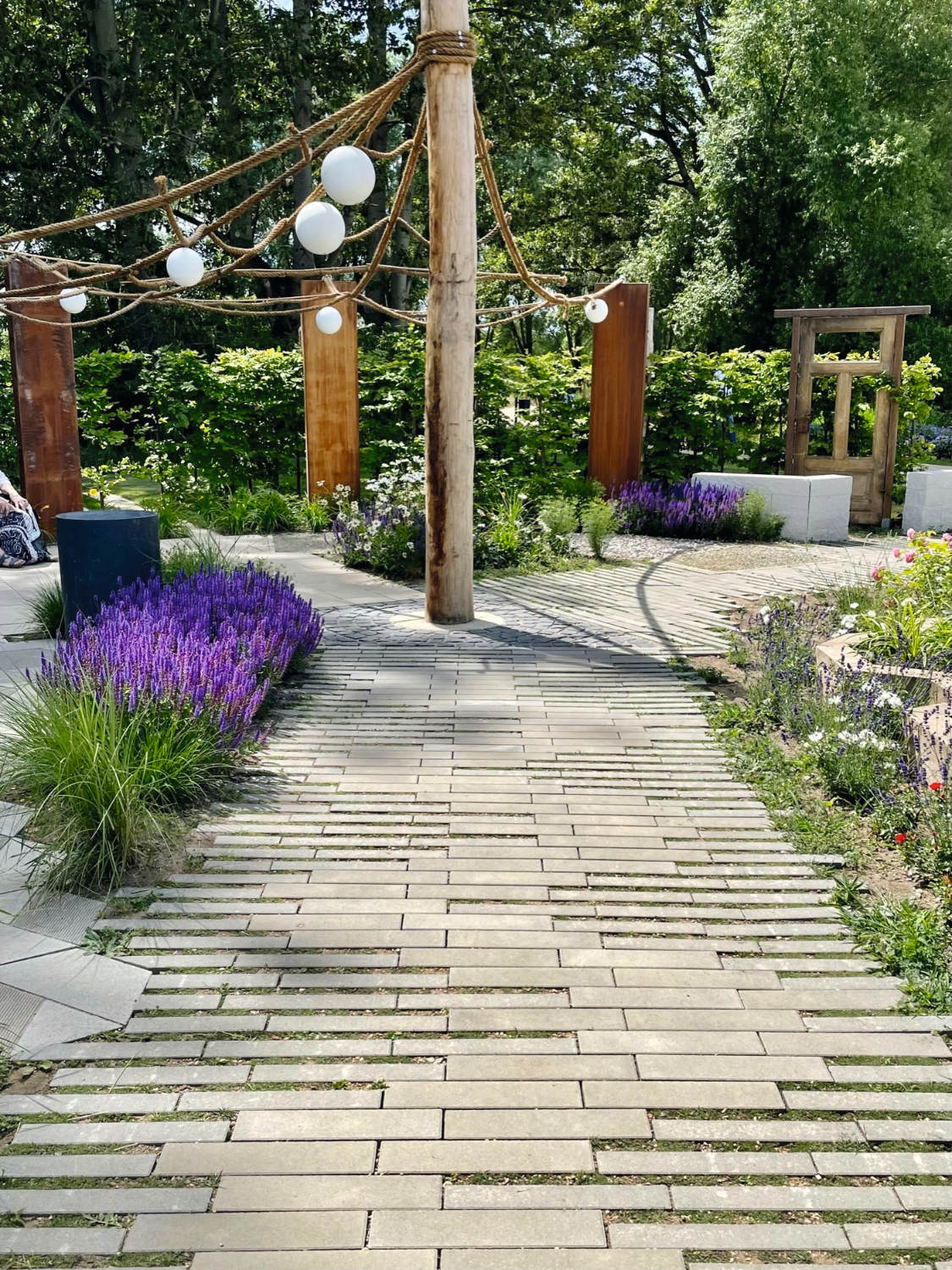
Antwerpen zwischen Barock und Design
Gartenkunst im Rubenshuis und Outdoor-Möbel der Region

Grünes Licht aus Italien
Beim Leuchtenhersteller Artemide hat Nachhaltigkeit Tradition

Flexibilität in der Gestaltung
Beispielhafte Projekte setzen auf Systembaukästen von Gira

Wasser und Beton
Neue Badeorte für urbane Hitzeinseln

MINIMAL MASTERS
Wie die Shaker mit klaren Werten und asketischem Stil das Design prägen

Gut geplante Badsanierung
Barrierefreie Bäder nachrüsten – so gelingt die Sanierung im Bestand

Plädoyer für Zirkularität
Ausstellung „WEtransFORM. Zur Zukunft des Bauens“ in der Bundeskunsthalle Bonn
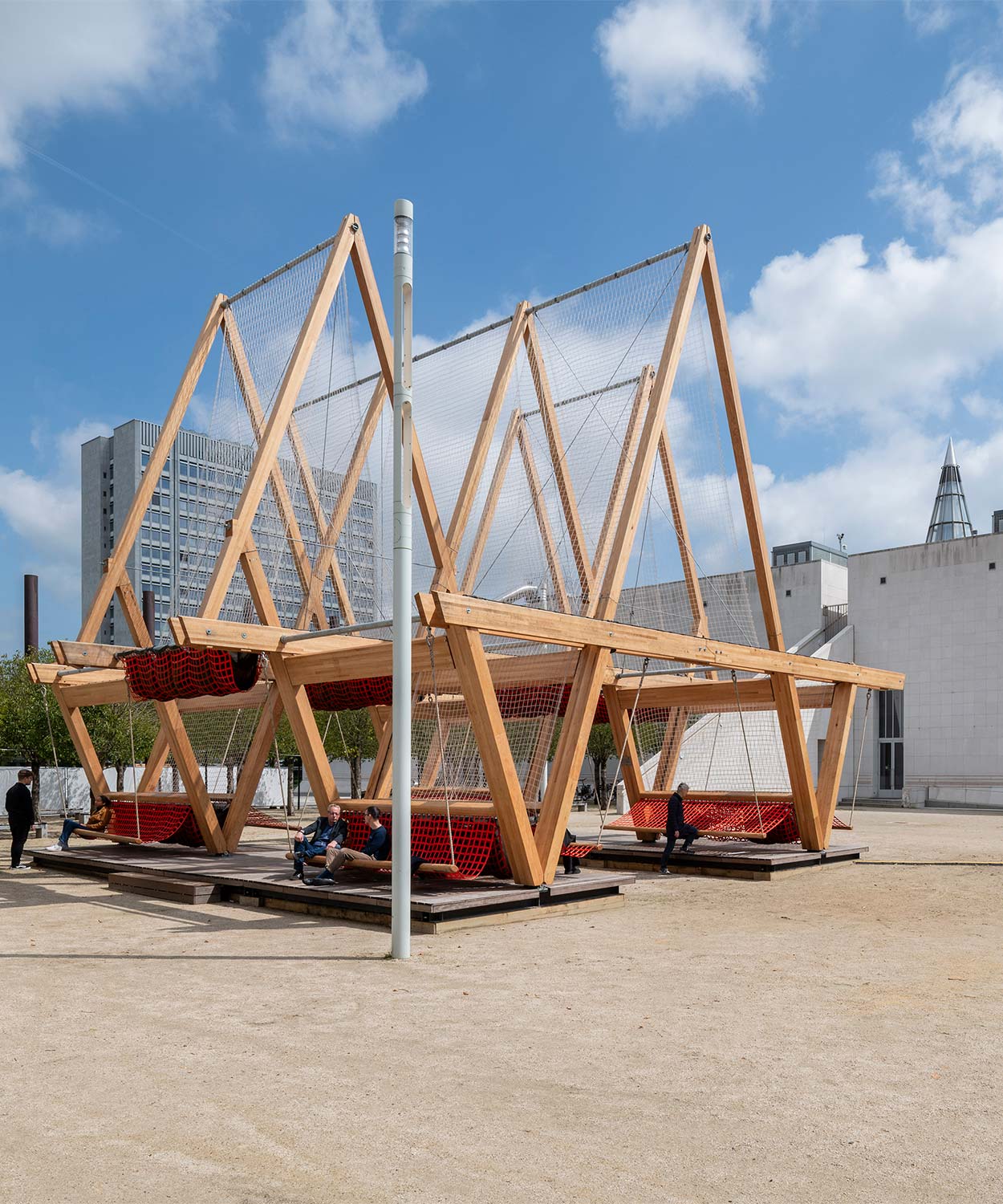
Händewaschen ohne Anfassen
Berührungslose Armaturen von VOLA für Hotels, Flughäfen und Badezimmer
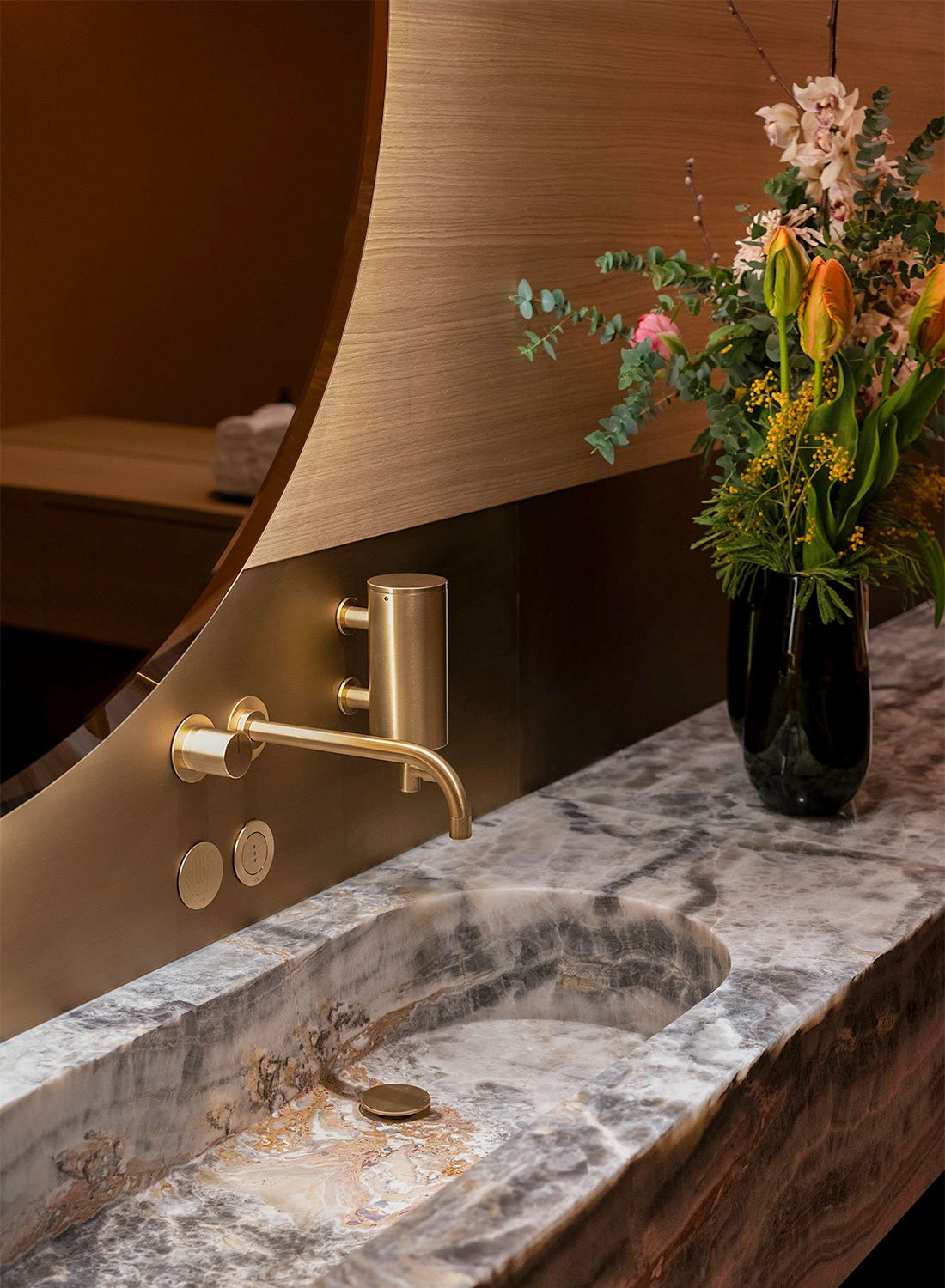
Schatz in der Fassade
Warum der Austausch historischer Kastendoppelfenster ein Fehler ist
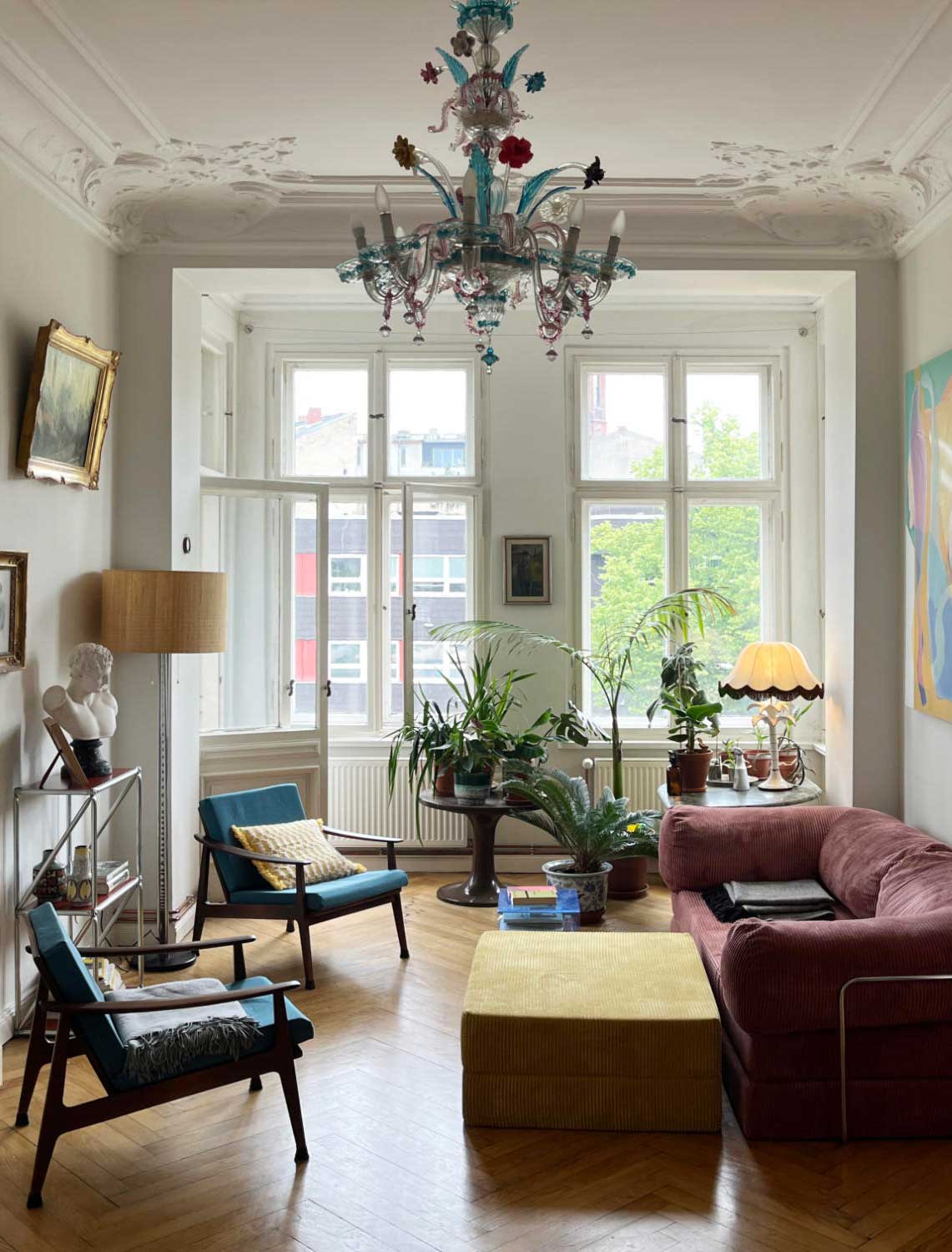
Zukunftsorientierte Gestaltung
Wie Brunner gutes Design mit verantwortungsvollem Handeln verbindet
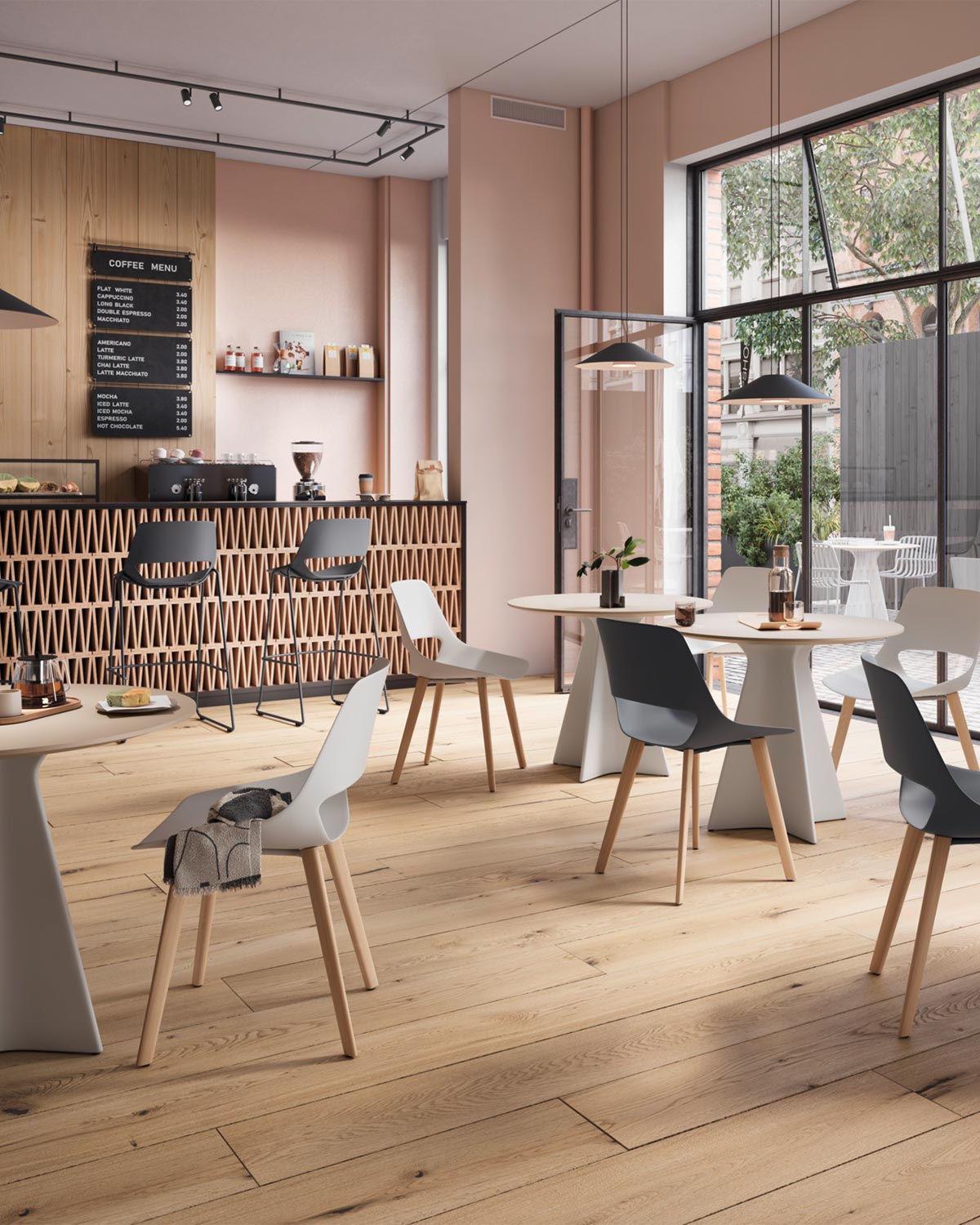
Von rau bis hedonistisch
Wie verändert die Kreislaufwirtschaft das Interiordesign?
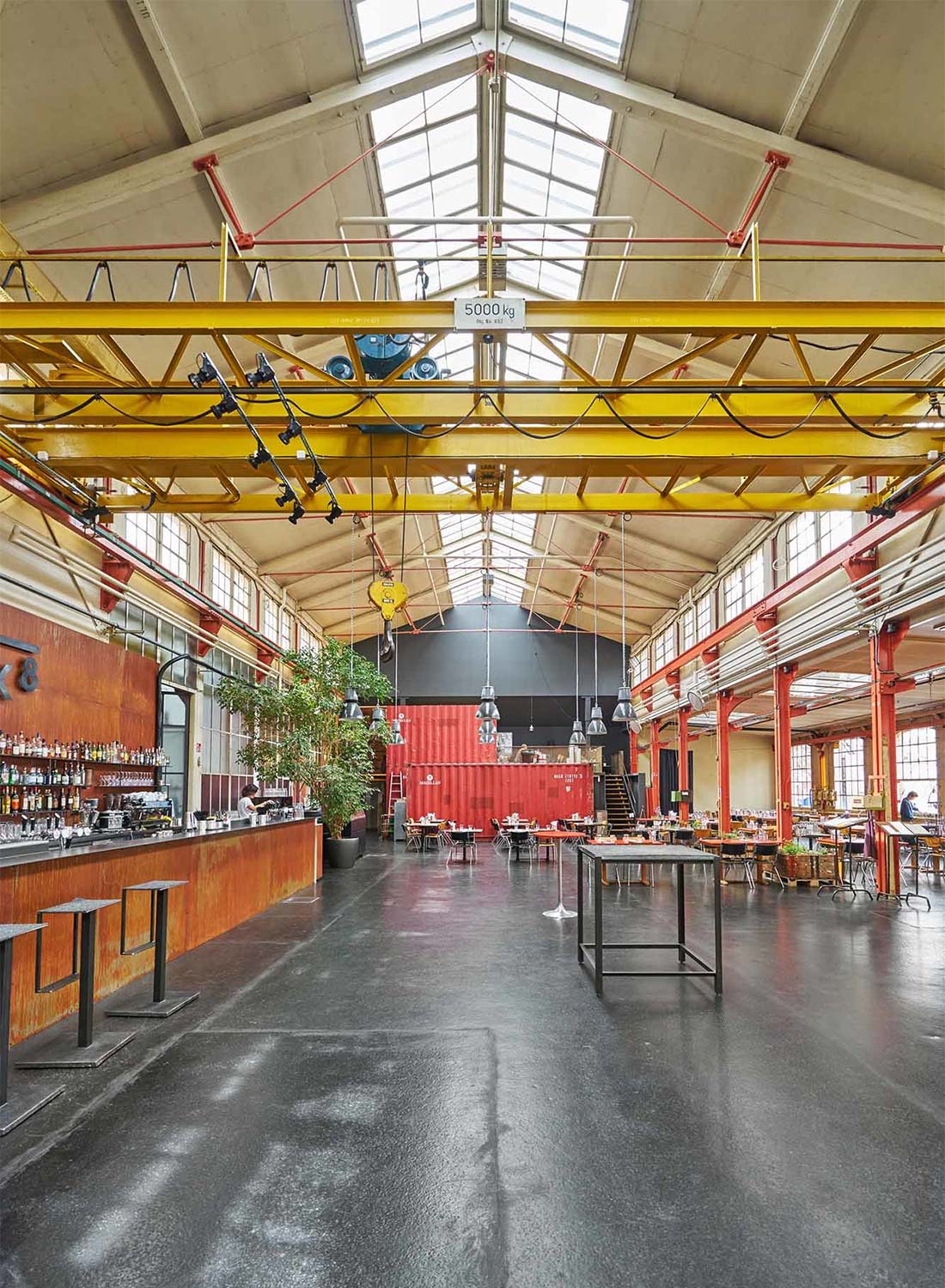
Neue Impulse setzen
DOMOTEX 2026 präsentiert sich mit erweitertem Konzept
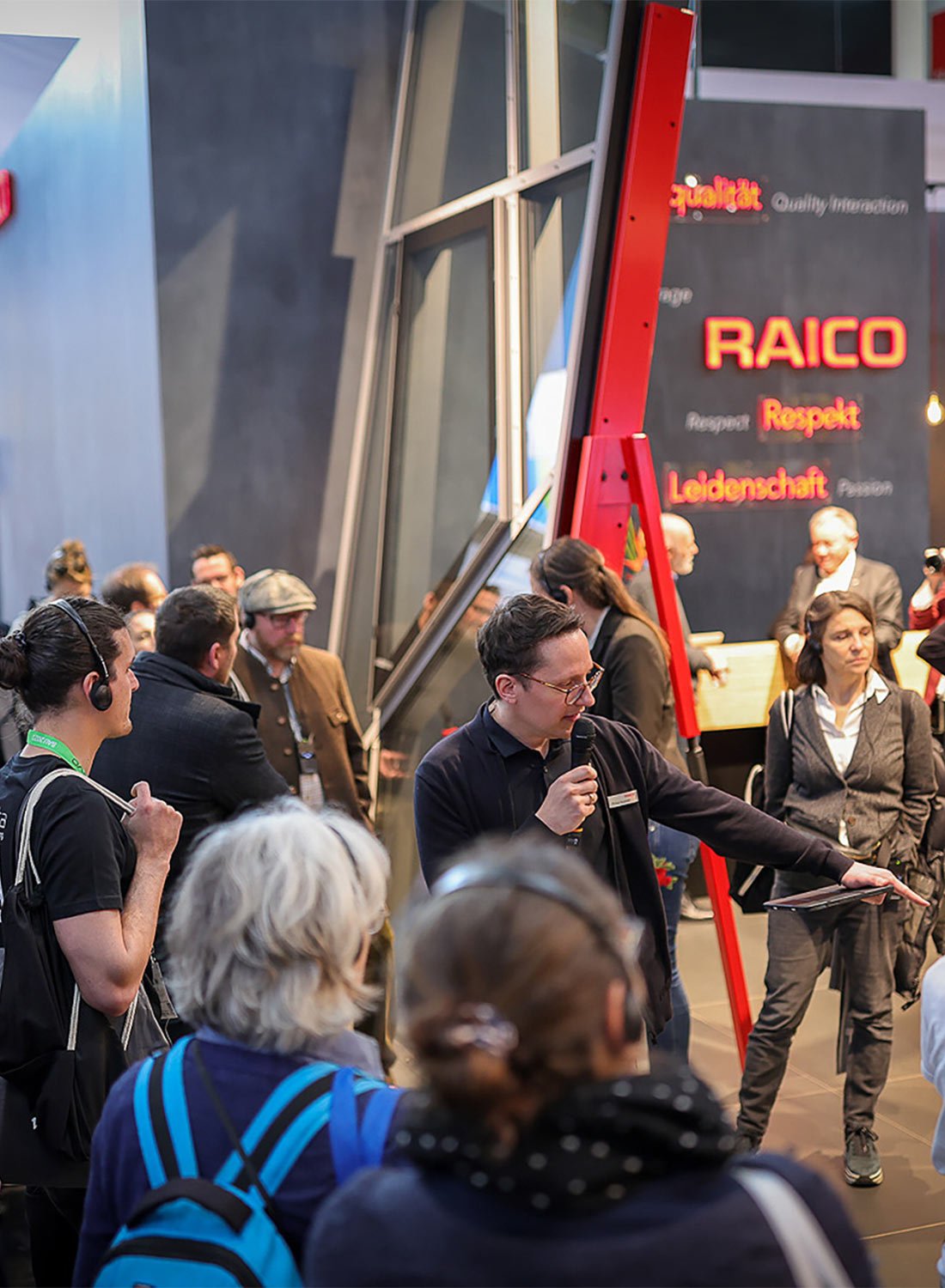
Nachhaltig und komfortabel
Mit einem archetypischen Bürostuhl revolutioniert Wilkhahn das ergonomische Sitzen
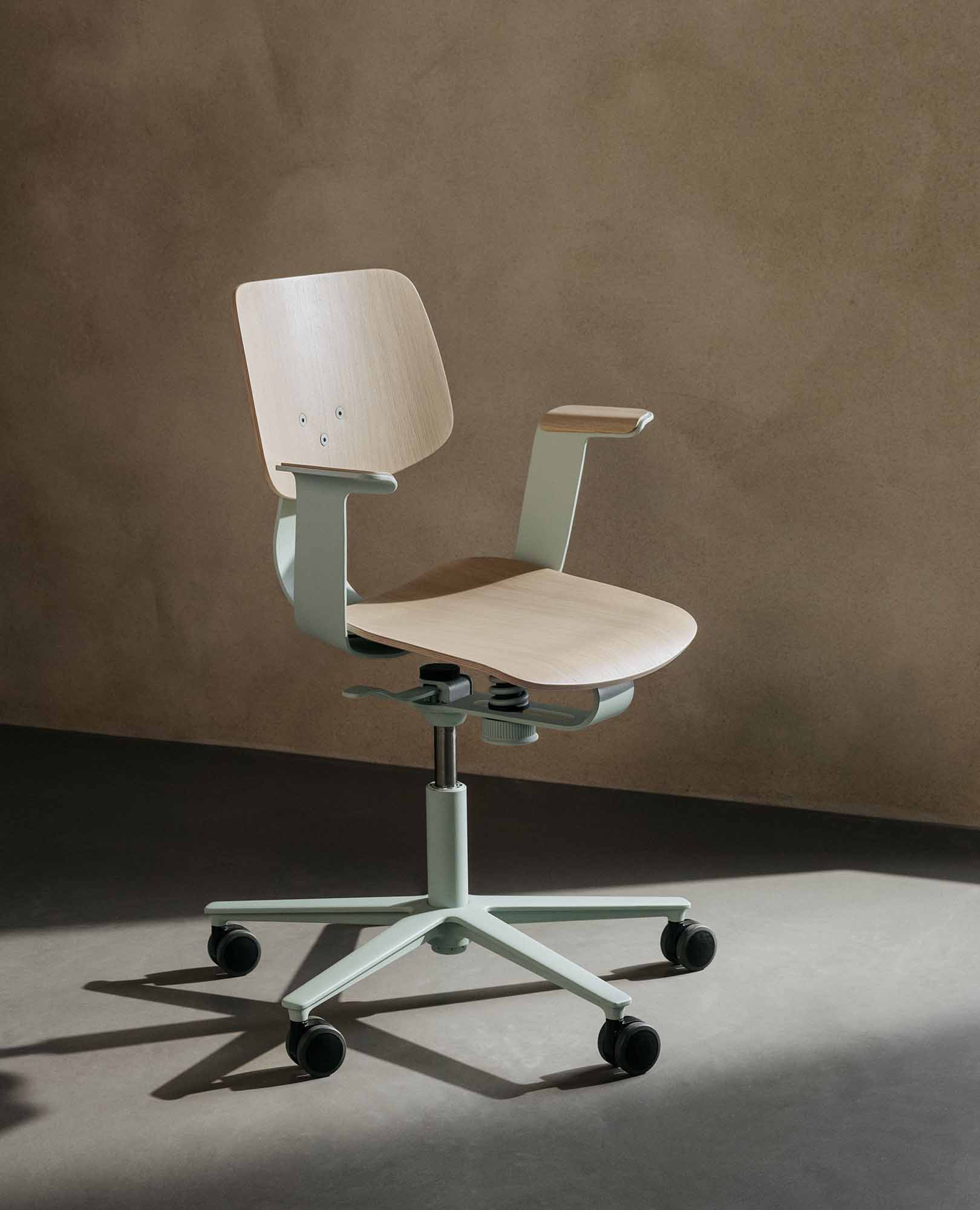
Büro im Kreis gedacht
WINIs nachhaltige Möbelstrategie am Beispiel einer Spanplatte
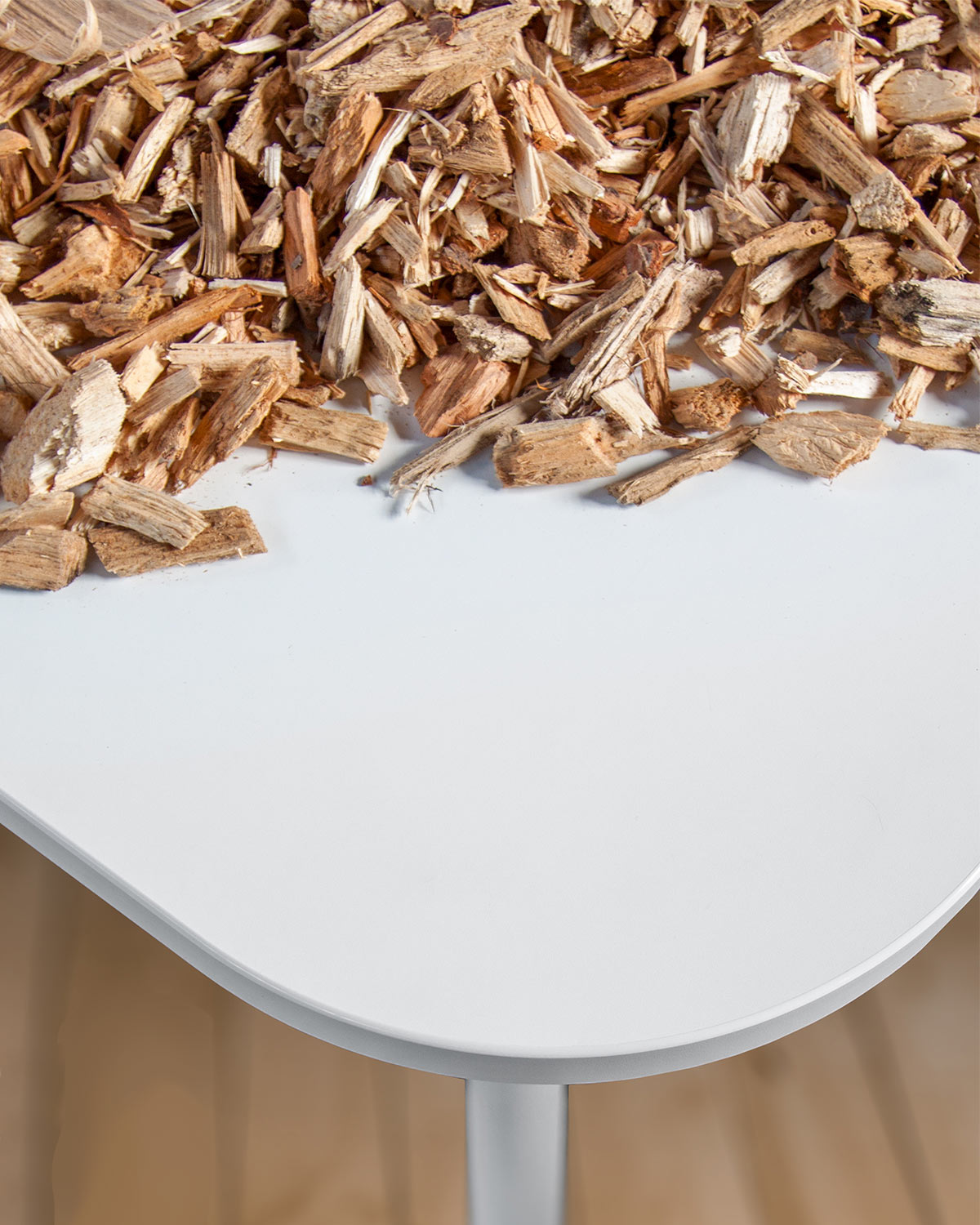
Der Stuhl, der CO₂ speichert
Mit einer Sitzschale aus Papier setzt Arper neue Maßstäbe für nachhaltige Materialien
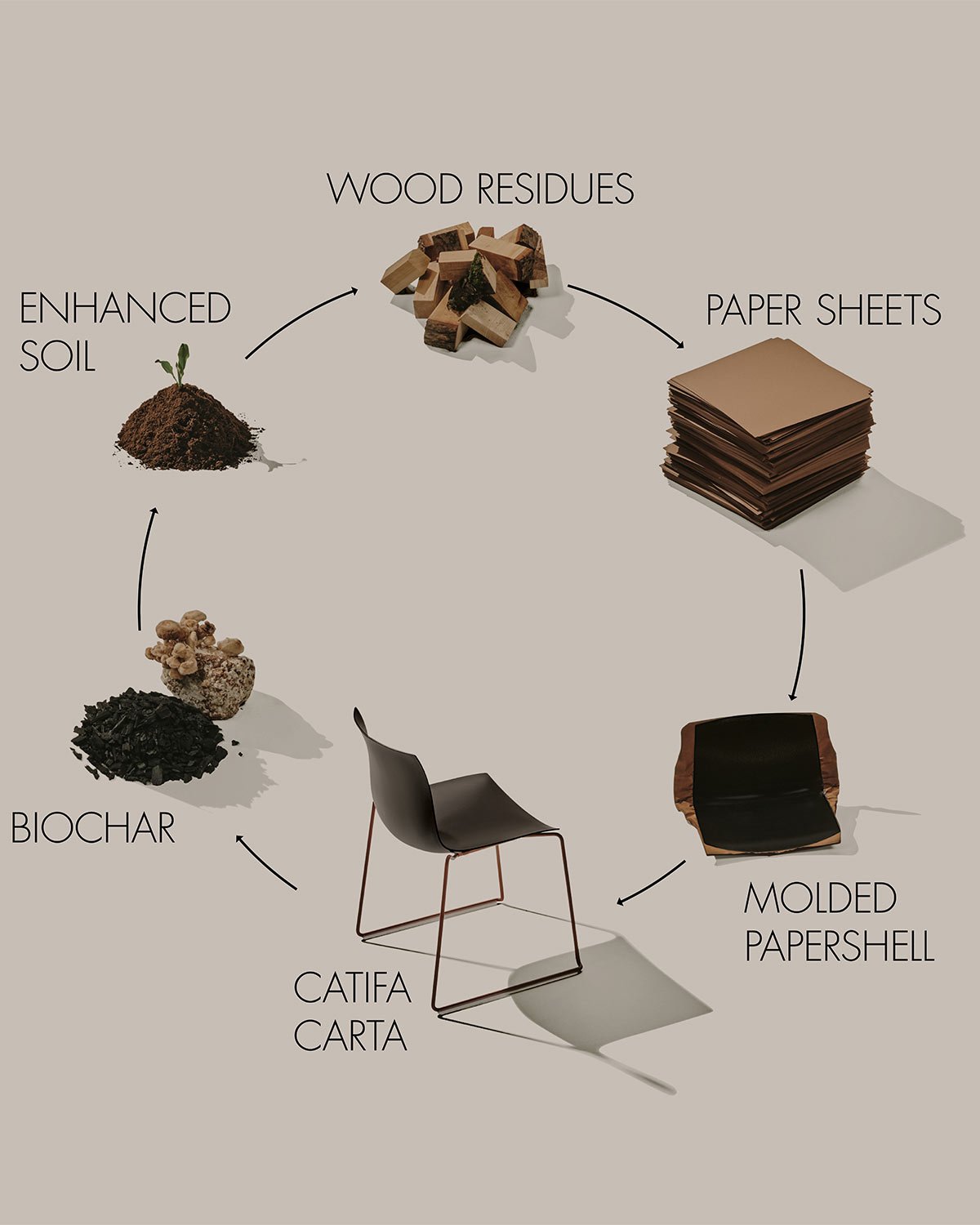
Zwei Marken, eine Mission
Wie Fellowes und Filex den Arbeitsplatz von morgen neu denken
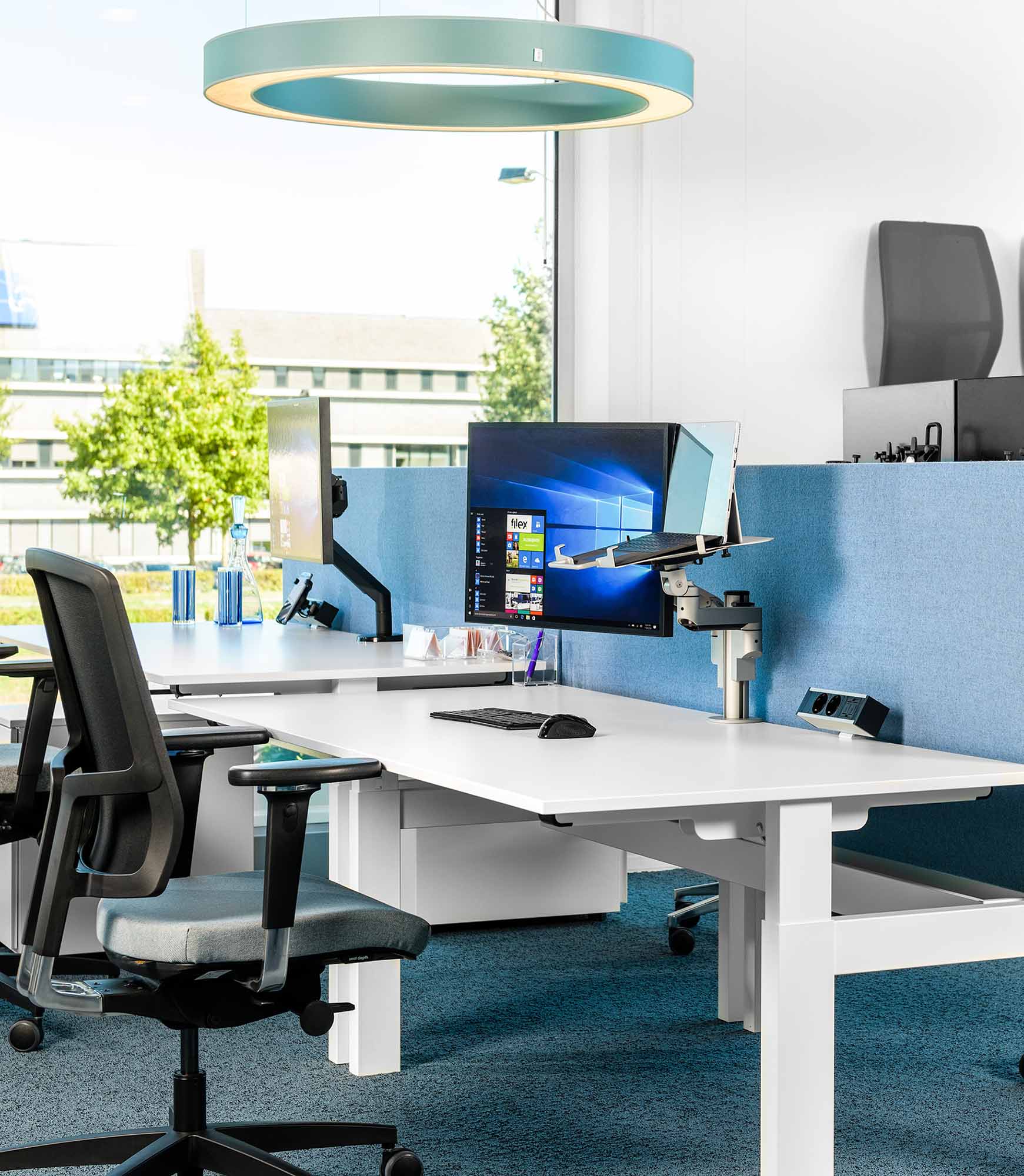
Außenräume und Innenräume
Wie die Architekturbiennale 2025 in Venedig neue Konzepte für ein Klima im Wandel entwirft
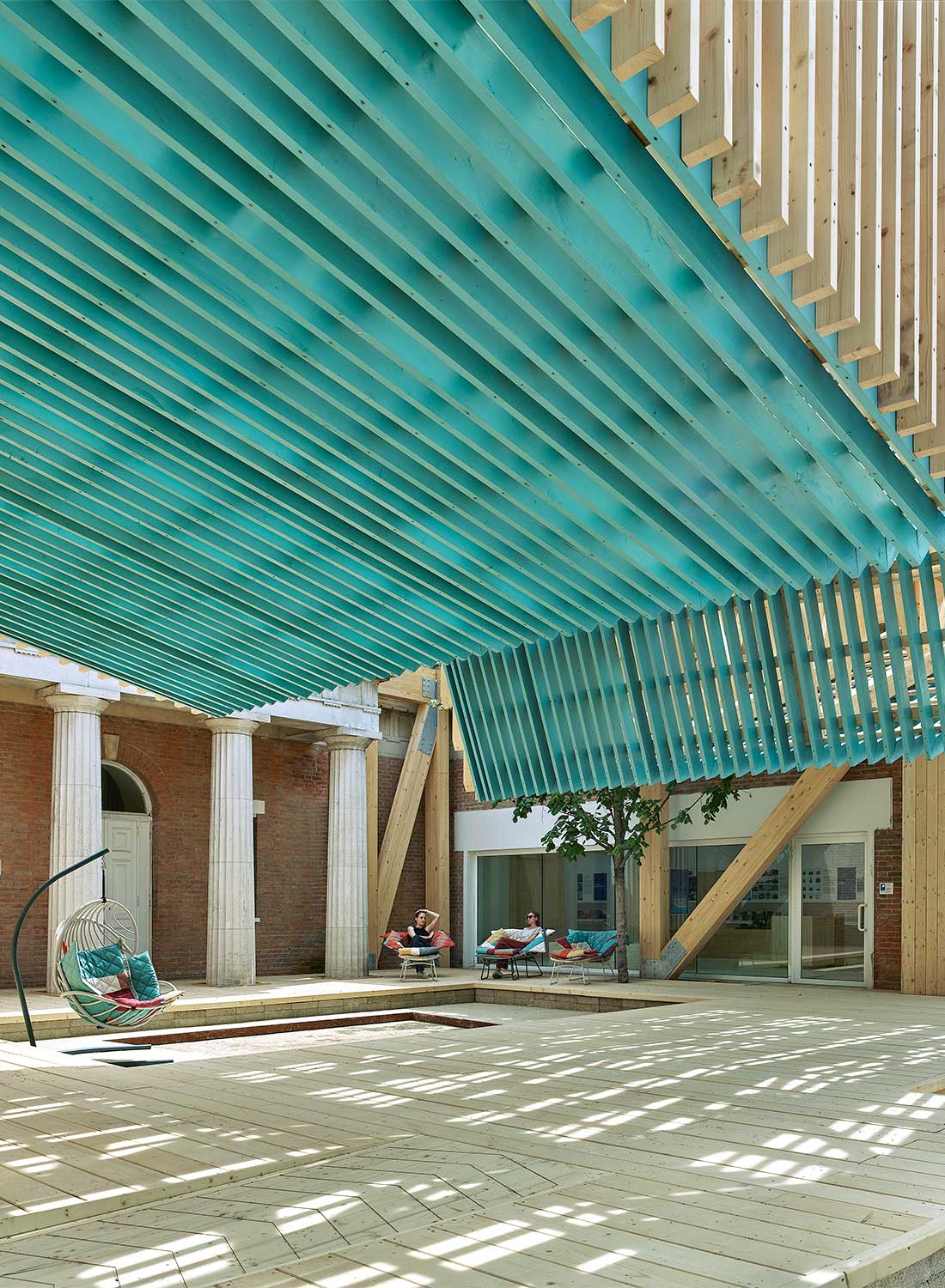
Digitale Werkzeuge in der Innenarchitektur
Wie ein Schweizer Büro Planung, Präsentation und Produktion verbindet
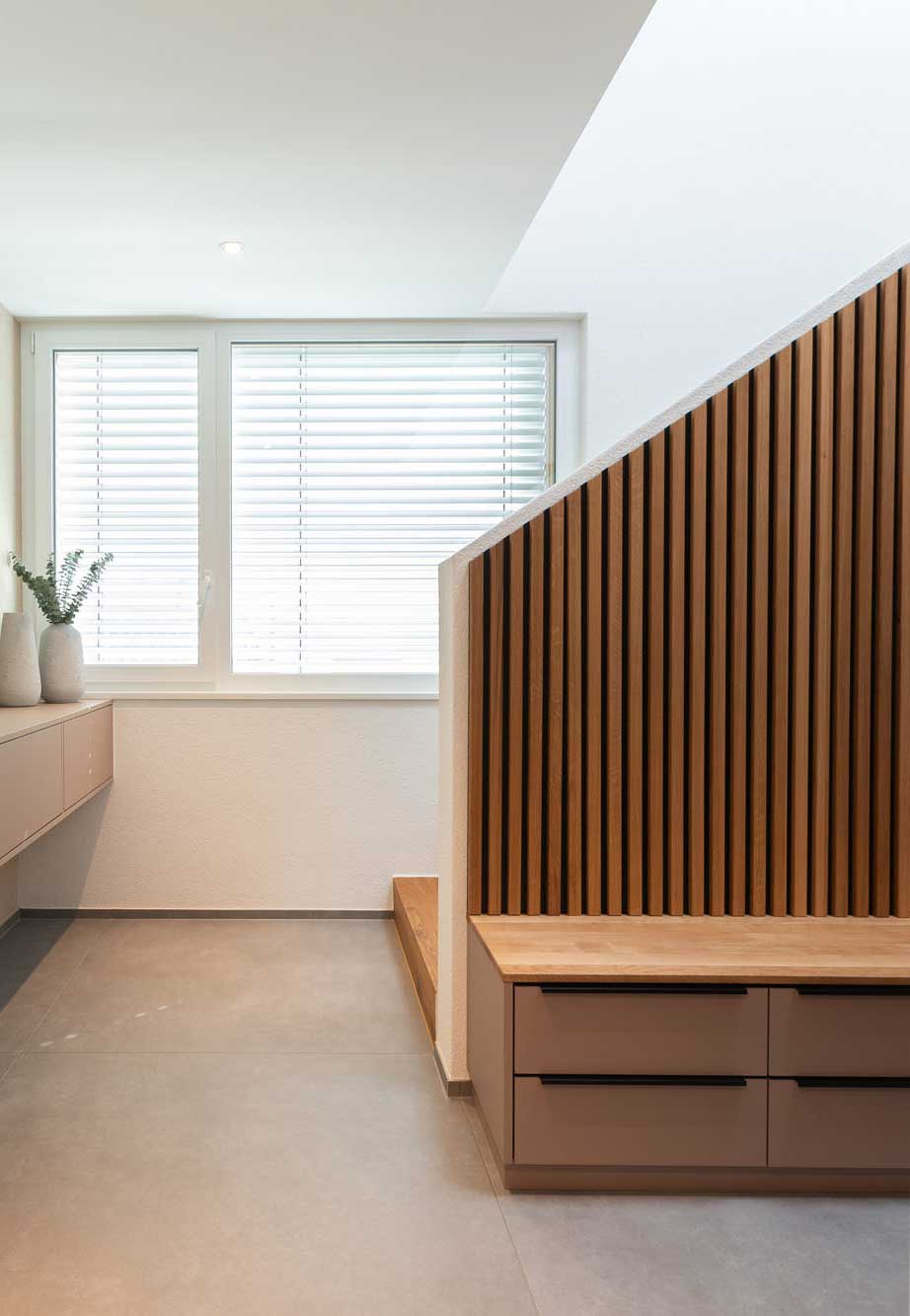
Wenn Möbel Wurzeln schlagen
Ausstellung mit USM Modulen bei der Architekturbiennale Venedig 2025
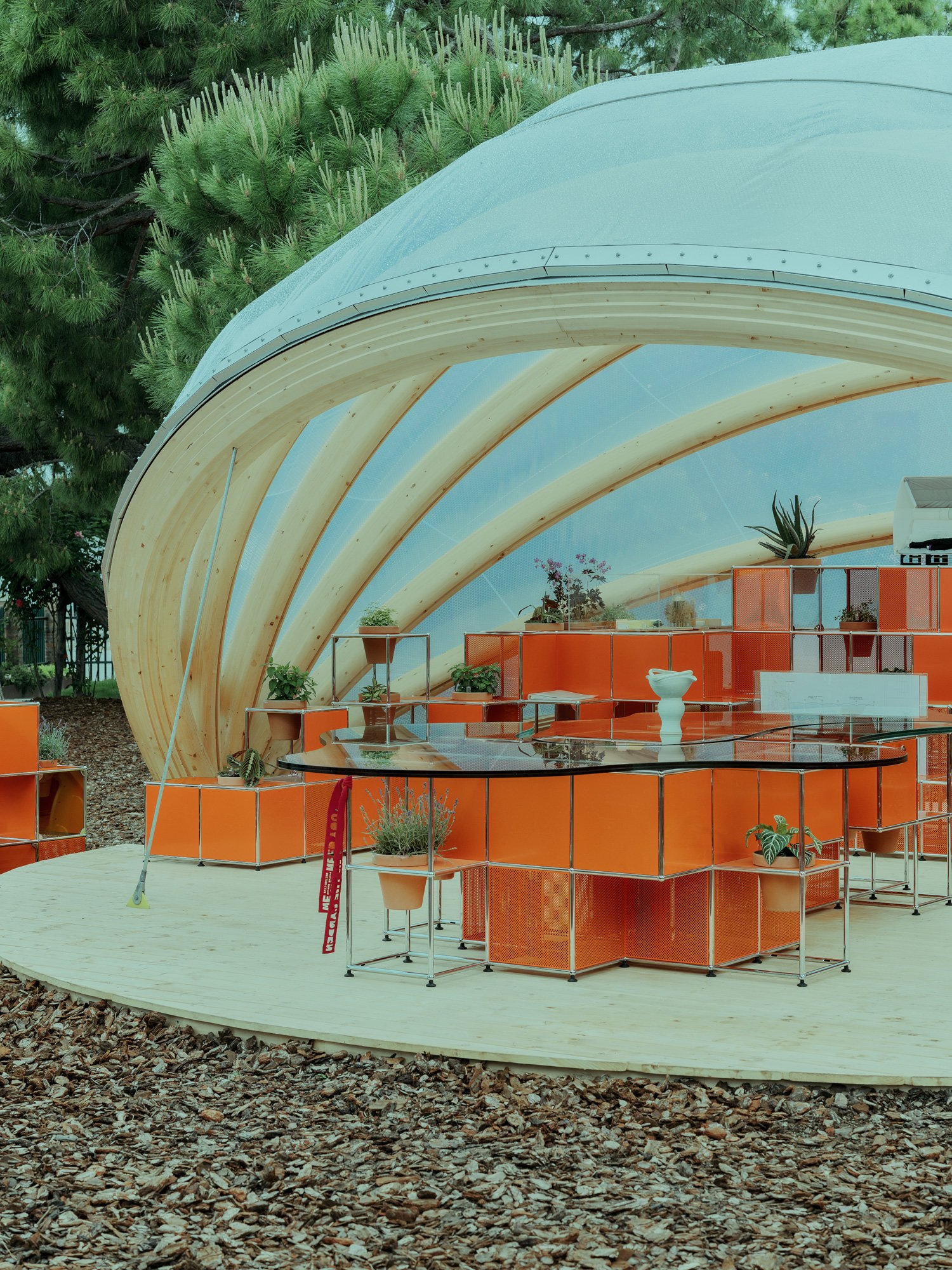
Natursteinästhetik in Keramik
Fünf neue Oberflächen erweitern das Feinsteinzeug-Programm des Herstellers FMG
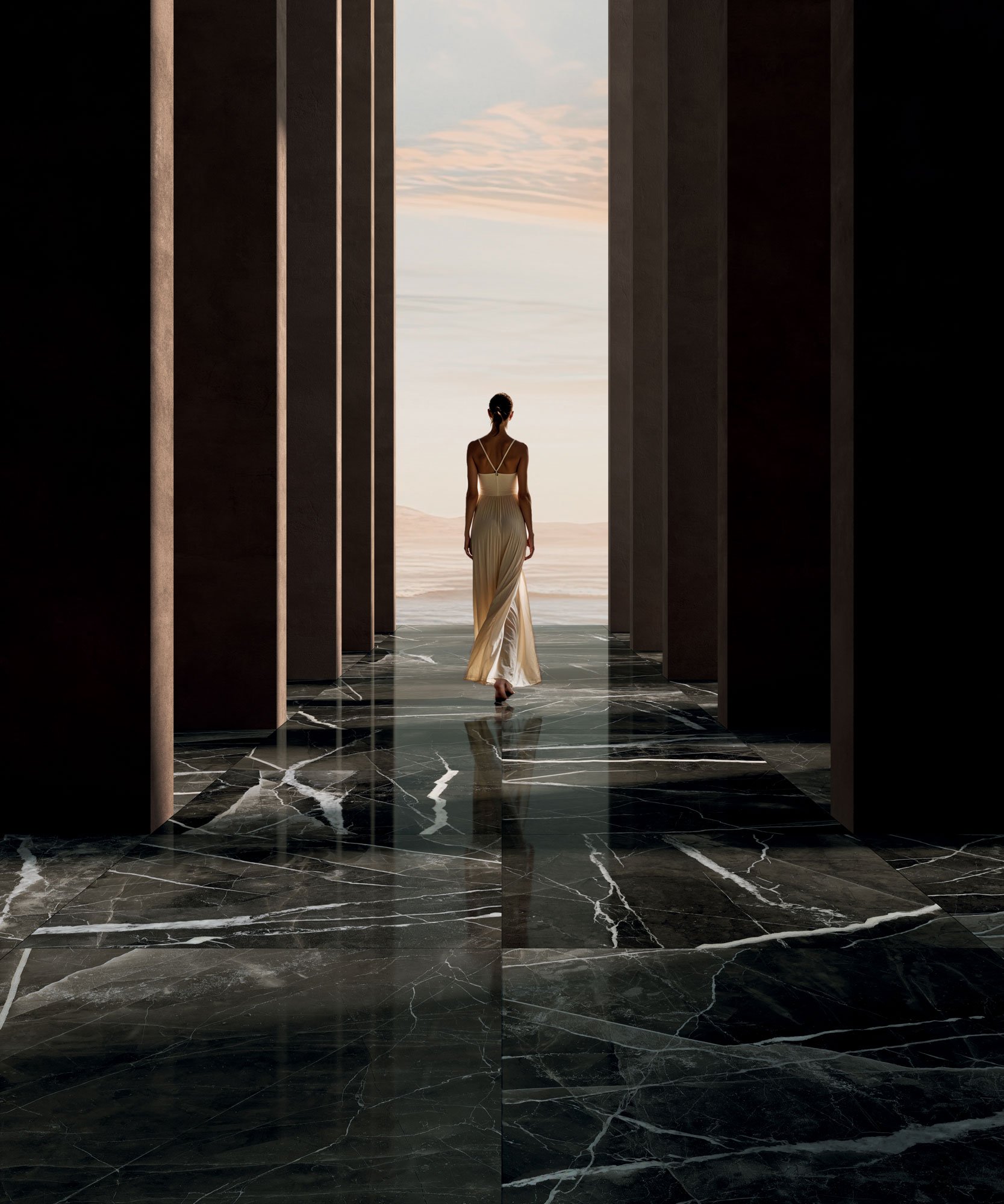
Creative Britannia
Unterwegs auf der London Craft Week und Clerkenwell Design Week
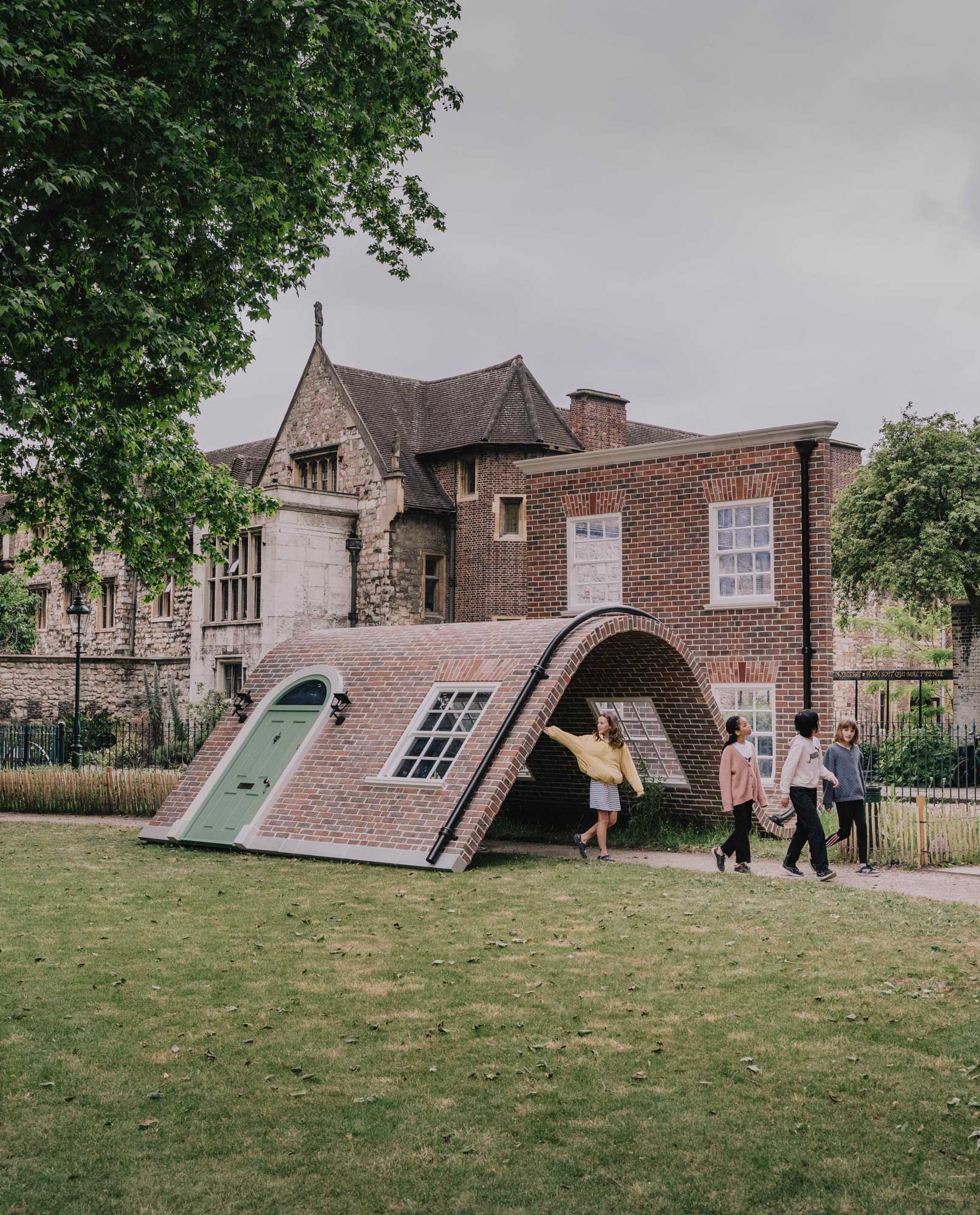
Best-of Licht & Leuchten 2025
Neuheiten aus Mailand: Euroluce und Milan Design Week
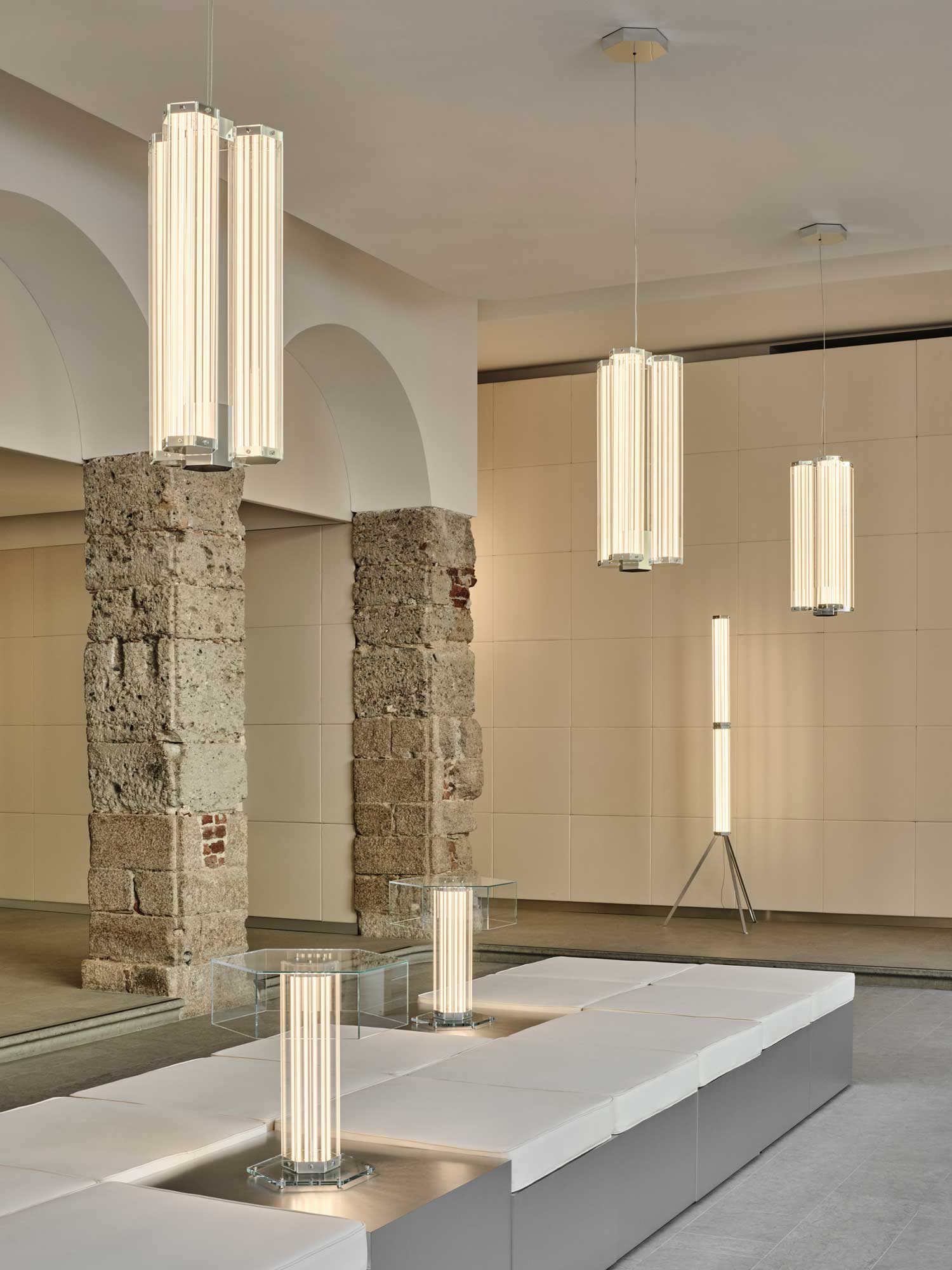
Diskurs statt Dystopie
Deutschlands Vision für klimaresiliente Städte auf der Biennale 2025 in Venedig
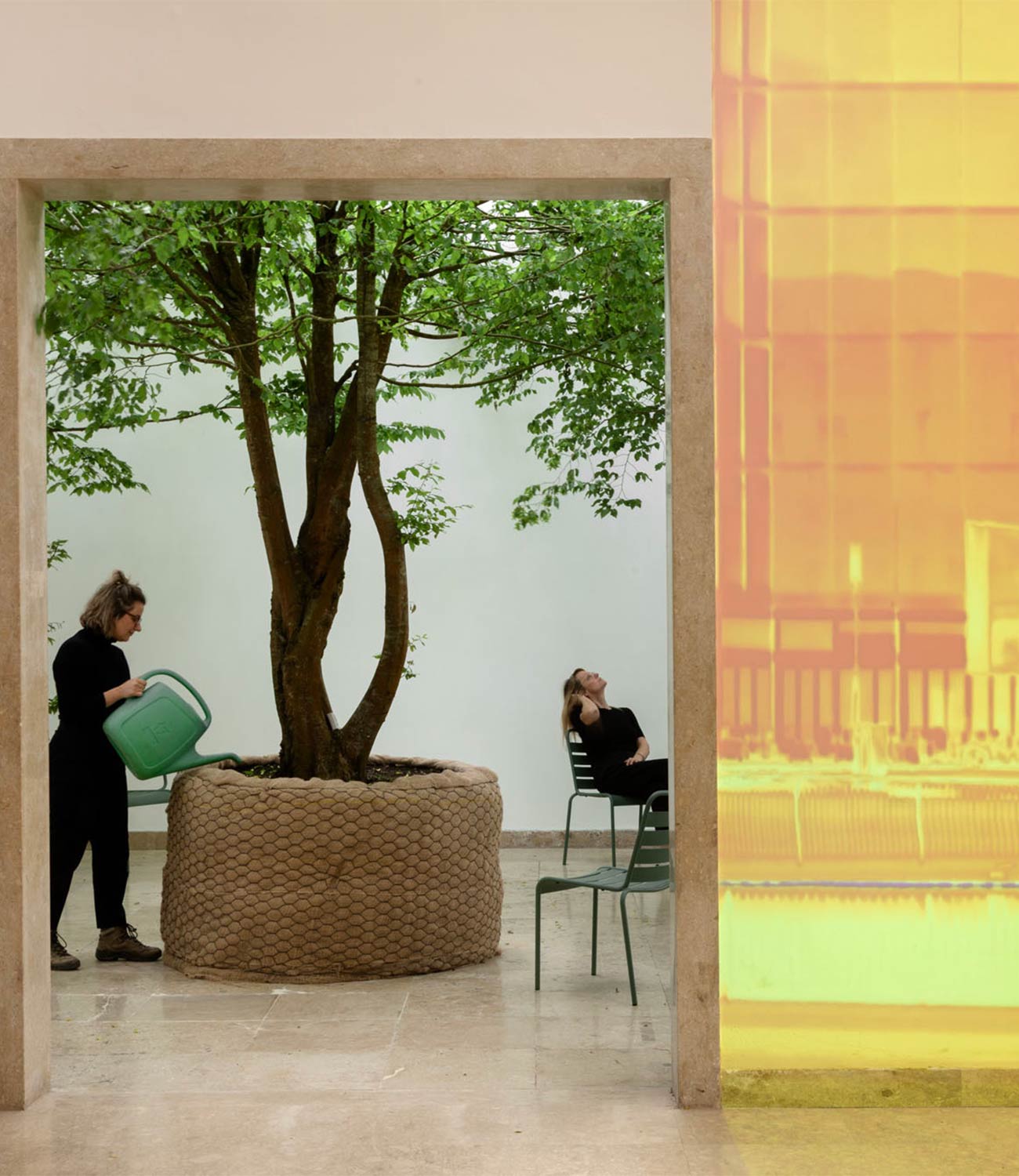
Auf stilvoller Welle
Ikonische Tischserie wave für exklusive Objekteinrichtungen von Brunner
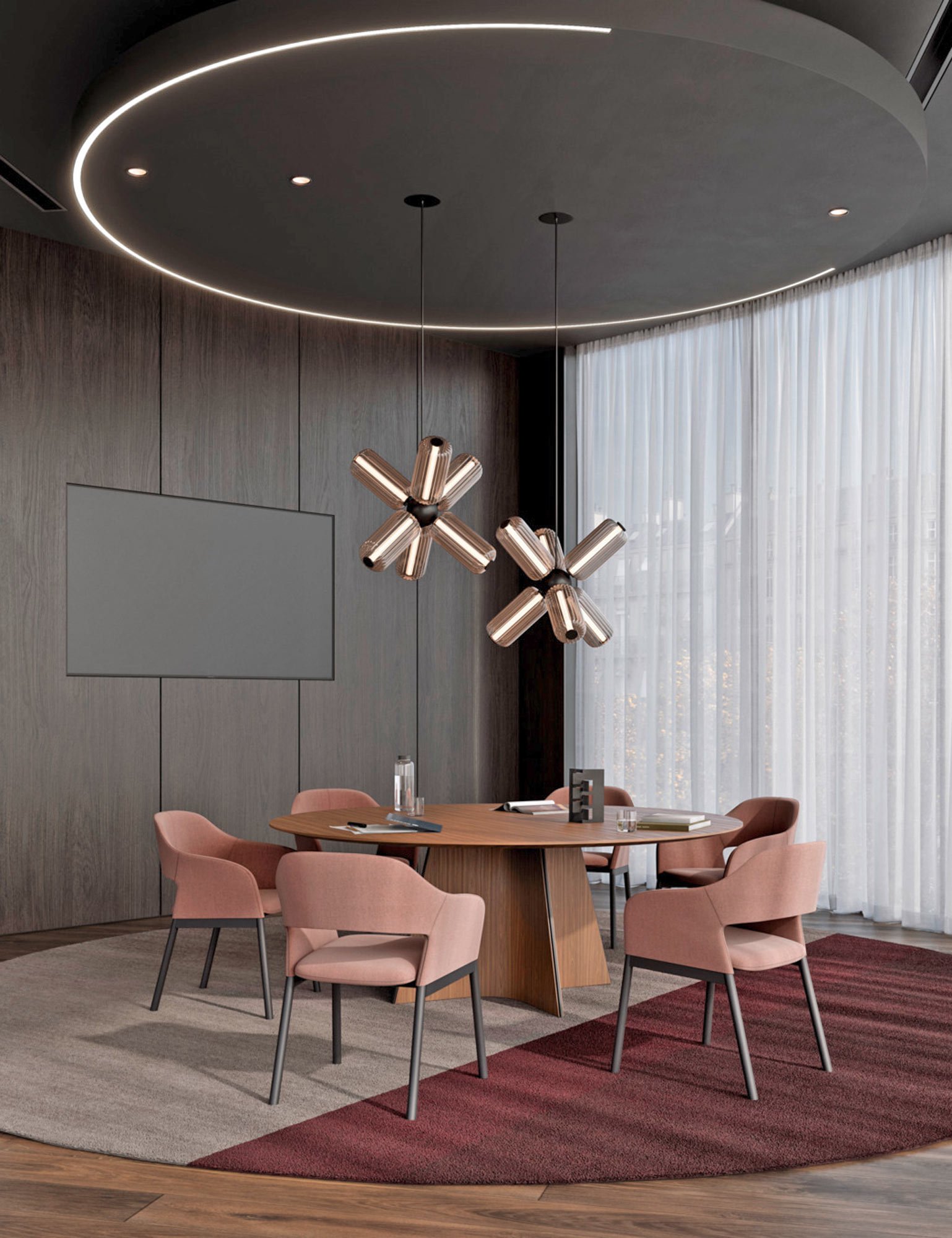
Analog sitzen, virtuell denken
Wie Interstuhl seine Designkompetenz ins Digitale erweitert
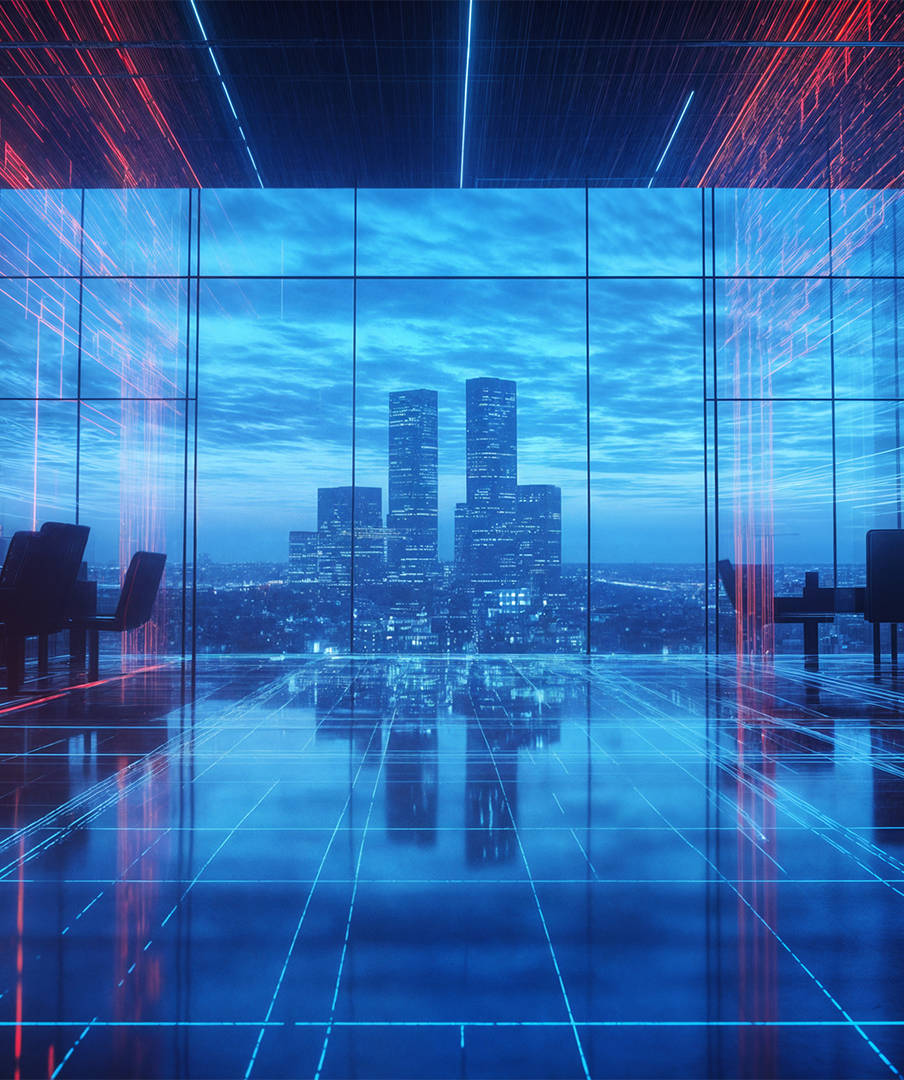
Wilkhahn Refurbishment
Ein zweites Leben für besondere Modus-Drehsessel
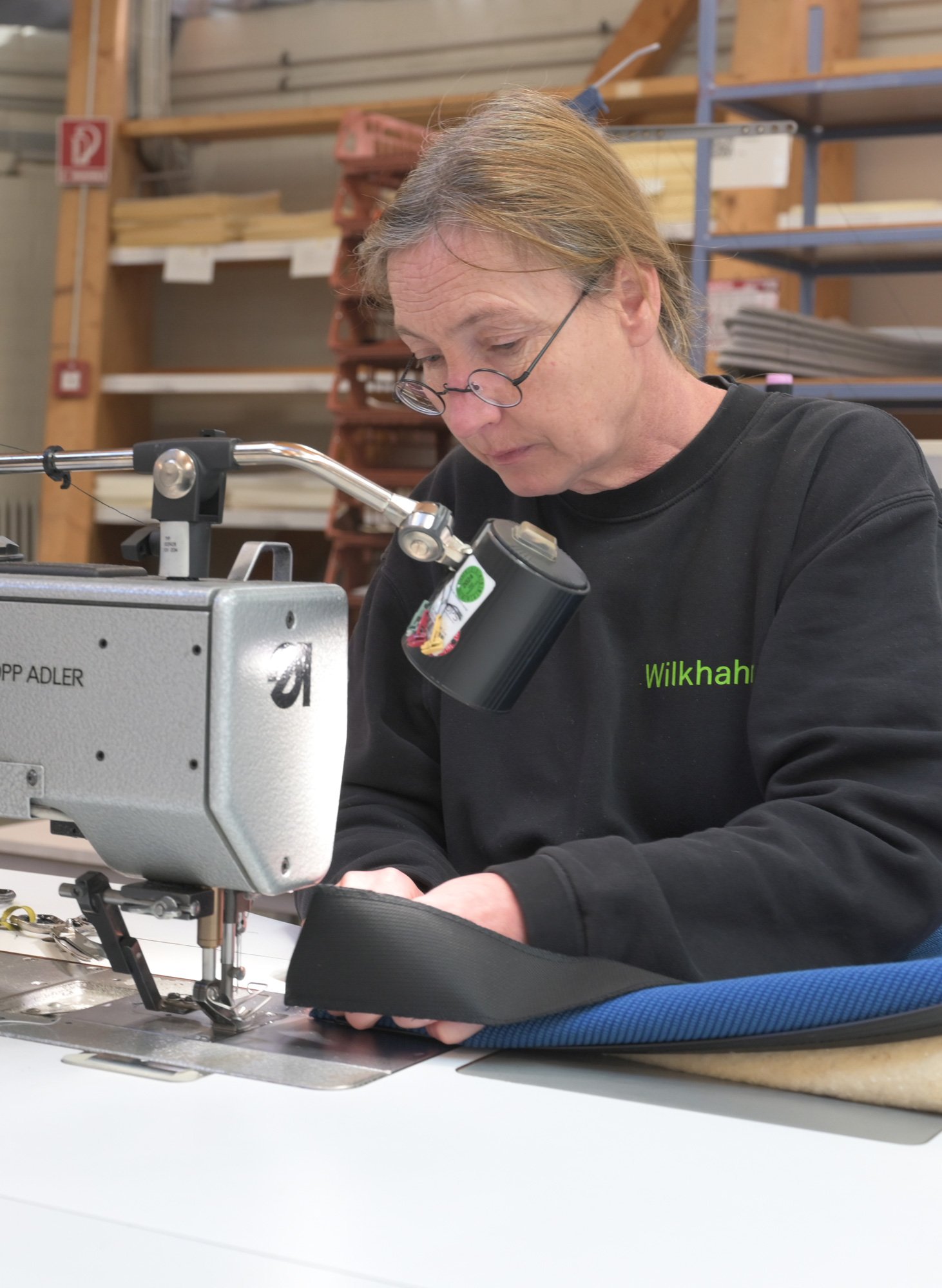
Spektrum der Ruhe
Wie nachhaltig sind farbige Möbel?
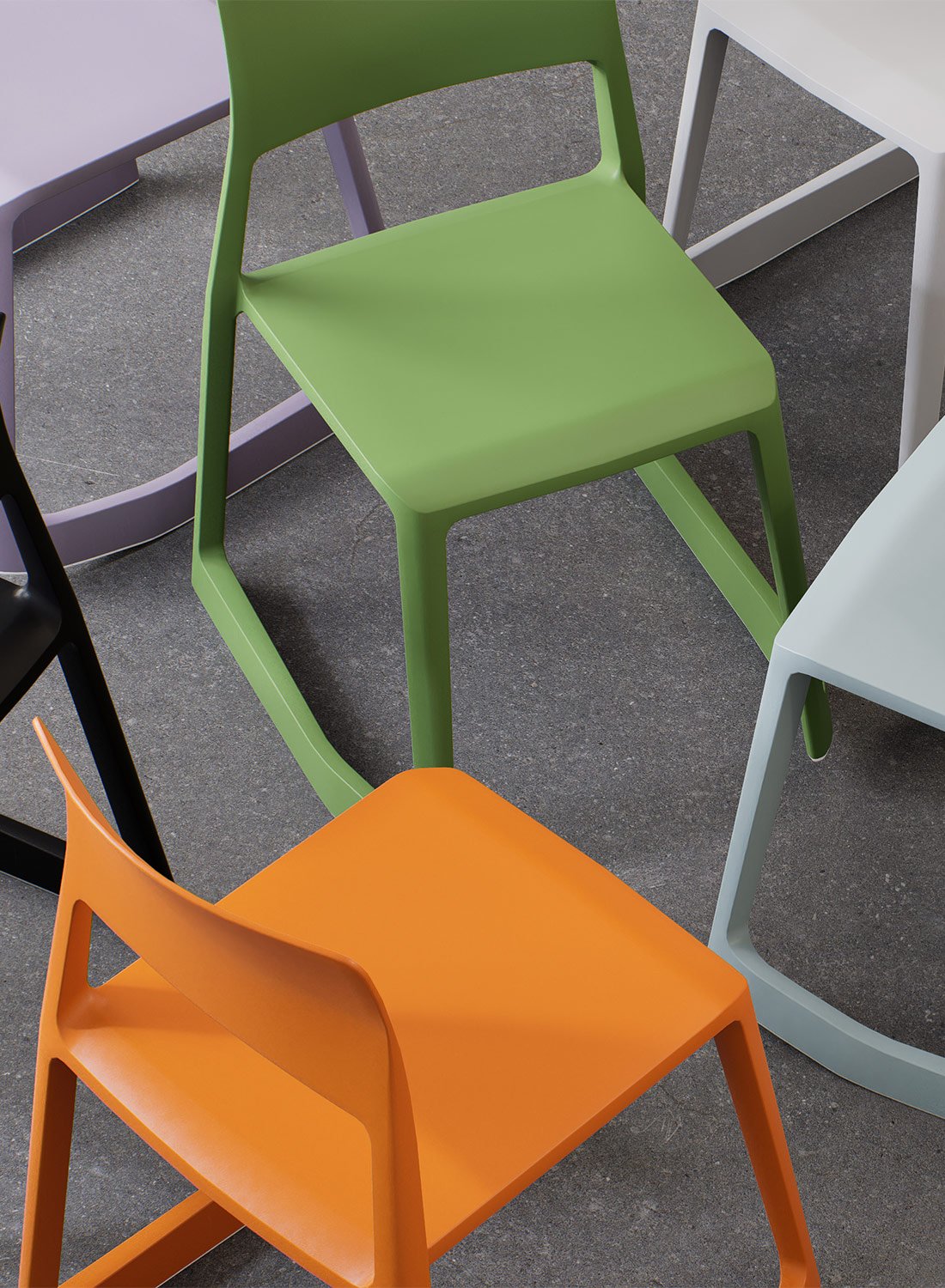
Genähte Systemmöbel
Raphael Klug macht Pappe zum schlüssigen Material für nachhaltiges Möbeldesign
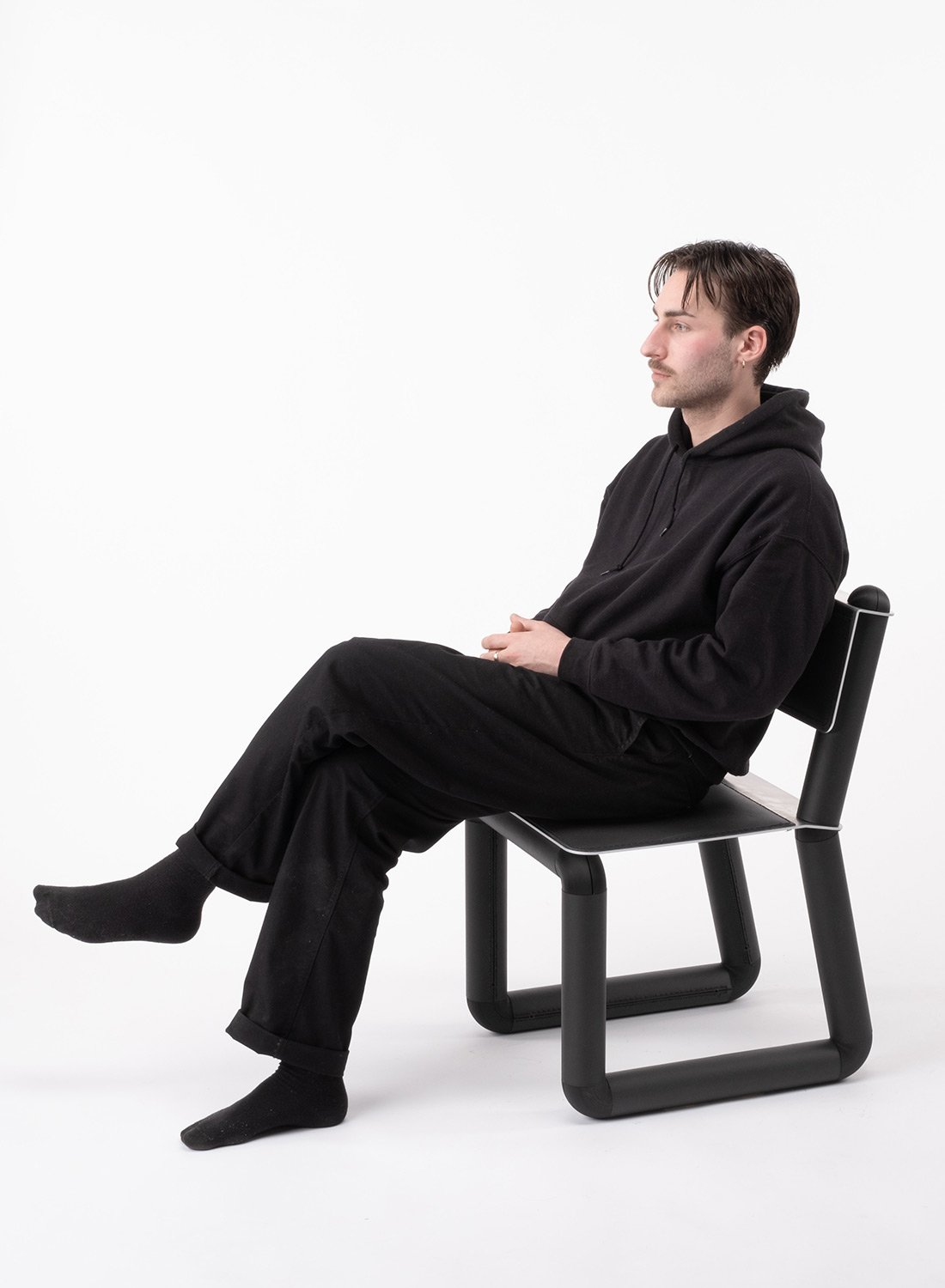